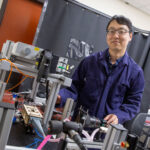
Industrial engineers develop new AI to elevate 3D printing
Feng Ju collaborates with industry and academic partners to create systems that print personalized, reusable furniture

In the future imagined by Feng Ju, interior designers will have artificial intelligence, or AI, tools to create everything from French provincial furniture to mid-century modern magic with a few keystrokes.
In the future imagined by Haddy, new décor won’t require new materials.
Ju, program chair of the highly ranked industrial engineering program in the School of Computing and Augmented Intelligence, part of the Ira A. Fulton Schools of Engineering at Arizona State University, is working with the team at Haddy, as well as with researchers at Oak Ridge National Laboratory and the University of Tennessee, Knoxville, to create artificial intelligence, or AI, tools and algorithms that make 3D printing faster, more sustainable and provide more accessible creative tools for designers and engineers.
The researchers have been studying large-format additive manufacturing, a term that refers to the 3D printing of industrial objects as large as boats and vehicles. Haddy is a successful furniture startup headquartered in St. Petersburg, Florida, where engineers are working collaboratively with interior designers to 3D print unique, customizable furnishings for their clients.
Haddy has teamed with academic partners to both improve their current manufacturing processes and develop innovative solutions for the future. Together, they have been busy conducting research in two areas. First, the team is creating AI tools that will enable 3D printers to work as quickly as possible without decreasing quality or increasing waste.
Then, they will develop a new AI platform — a kind of ChatGPT for industrial engineers — that will allow furniture designers to 3D print new designs by typing their ideas into a prompt. The technology, funded by the U.S. Department of Energy and the Manufacturing, Automation and Data Engineering Science and Technology Center at ASU, promises to help designers deliver truly customized furniture that is as unique as their clients.

Large format additive manufacturing machines, or 3D printers, layer materials in a predefined form. A thermal camera monitors the temperature of the material layers as printing occurs to ensure that the material does not become too hot. Image courtesy of Haddy
Cooling off a hot topic
In large-format additive manufacturing, a machine places layer after layer of materials, such as plastics, resin or metals, on top of each other in a form defined by a set of instructions fed to the printer by a computer. Companies using this technology want their printers to work fast to ensure economical production that benefits consumers.
The current challenge lies in maintaining the proper temperature.
Dylan Hoskins, senior engineer at Haddy, compares this process to baking.
“You don’t want something to be underbaked because then it’s just going to turn to mush,” he says. “You don’t want something to be overbaked because then it’s too hard. In both cases, the result is useless.”
This problem exists in the inverse for large-format additive manufacturing. If the printer works too fast, the material becomes molten, collapses on itself and can’t bear any weight. But if the printing process is too slow, materials don’t bond and easily come apart. Ju adds that factors like air temperature in the factory can also play a role.

3D printed materials collapse when printed too fast and debond when printed too slowly. Feng Ju and his team are creating artificial intelligence systems to help machines learn to self-adjust their printing pace. Images courtesy of Feng Ju
The AI system that the team is creating will take data from thermal cameras and sensors, combine it with environmental information, and then train the 3D printer to adjust its speed as needed. Ju, who is also a Fulton Schools professor of industrial engineering, sees this as an important part of creating a performance guarantee that produces a consistent result and frees engineers to be as productive as possible.
“The concept here is to help the machine make real-time decisions automatically for the printing process, speeding up when it can and slowing down when it has to,” Ju says.
This will enable Haddy to maximize the amount of deliverable furniture for clients and ensure that their quality standards are always met.
Bringing new AI tools to the table
For the next phase of the work, the team will turn their attention to the creation of generative artificial intelligence tools for furniture designers. Generative AI is a type of technology that enables users to enter input, like text and images, and prompt the computer to produce new content. Examples of generative AI include using Midjourney to generate new images or ChatGPT to write text. These applications use large language models, which are huge repositories of information about specific prompts users are likely to enter and what the computer should do in response.
Here, Ju and his fellow researchers will combine the type of production engineering information that furniture designers are likely to need with large sets of language data that will help the computer understand the prompts provided by the users. They will develop sets of algorithms or rules that the machines will use to do their work.
The result will be like having a team of designers and production engineers always on call.
Haddy designers will be able to describe their ideas in plain language and the AI system will convert the text into a set of instructions for the printer, seamlessly blending function and aesthetics.
Ju notes that the purpose of the tools is not to replace jobs being done by people, but rather create opportunities for more customized, personalized manufacturing systems that don’t yet exist.
“The dream here is to make it easy and affordable for clients to have furnishings that are truly made with their unique needs in mind,” Ju says.

In the future, furnishings made by Haddy will be able to be returned to the company where materials will be recycled and turned into new pieces. Clients can then have new décor without consuming new materials. Image courtesy of Haddy
Your current table could become your next chair
In one especially exciting aspect of the research, Ju and his team will collaborate with Haddy to provide sustainable solutions that can be applied throughout the entire life cycle of the large-format additive manufacturing process.
They will work with Haddy to create furnishings that can be truly repurposed.
The company has already begun its move toward using only recycled materials during its manufacturing process. However, it will soon begin placing a near-field communication, or NFC, tag in each piece of furniture it prints. These tags store small amounts of data and can communicate only with a nearby device, typically via Bluetooth technology. The process of interacting with an NFC tag is similar to scanning a barcode.
For Haddy, the tags will contain basic information about each printed piece of furniture, identifying what the item is and the materials from which it was made. The concept is that users will be able to scan the NFC tag and then potentially return the item to the company, where the piece would be ground up. The materials would then be used to print a different piece of furniture purchased by the client.
Thanks to new AI tools that will let Haddy quickly print items and furniture designers easily design new pieces, you might be sitting in the last chair you’ll ever need, but one that can be remade, endlessly fresh and always according to your current style.
Hoskins says these efforts are an important aspect of Haddy’s environmental focus.
“We want to do what we can to make sure that materials and plastics don’t end up unnecessarily in a landfill or in the ocean,” Hoskins says. “So, we’re trying to properly incentivize customers to reuse and reprint their furniture.”
Not part of the furniture
Next, Ju and the researchers will present their ideas at the Manufacturing Science and Engineering Conference held in June in Knoxville, Tennessee. At the event, which is considered the foremost annual forum for the scholarly exchange of advanced manufacturing research knowledge, the team will discuss two papers based on their work and gather feedback from other experts.
Ross Maciejewski, director of the School of Computing and Augmented Intelligence, believes that these kinds of collaborations benefit students, professional engineers and businesses.
“This is an important example of the power of working with industry partners and other research organizations,” Maciejewski says. “It demonstrates how the industrial engineering program in the Fulton Schools creates impactful results. Our students have access to a world-class faculty team whose members are role models for how to apply our curriculum in the real world.”